Point de commande et procédure de cycle de commande : la comparaison directe
Quels sont les avantages et les inconvénients des procédures de point de commande et de cycle de commande ? Quelles sont les conditions qui plaident en faveur de l'utilisation de la procédure du cycle de commande et celles qui plaident en faveur de la procédure du point de commande ? Le tableau suivant fournit des informations :
Procédure de point de commande | Procédure de cycle de commande | |
---|---|---|
Avantages |
|
|
Inconvénients |
|
|
Utilisation |
|
|
La procédure de point de commande en détail
La procédure de point de commande diffère de la procédure de cycle de commande par des caractéristiques et des particularités essentielles. l existe également différentes variantes d'utilisation. Les caractéristiques les plus importantes peuvent être résumées de la manière suivante :
Orientation sur la quantité :
La procédure de point de commande est principalement contrôlée par la quantité. Concrètement, cela signifie qu'une commande est déclenchée dès qu'un certain niveau de stock préalablement défini est atteint - le soi-disant stock d'alerte. Les dates de commande sont ainsi variables et elles ne sont pas déterminées à l'avance. La méthode du point de commande nécessite une vérification du stock actuel après chaque sortie de marchandises.
Stock d'alerte :
Le stock d'alerte est généralement déterminé à partir d'un stock de sécurité préalablement défini et des quantités de consommation typiques jusqu'à la livraison de nouvelles marchandises. En principe, ce qui suit s'applique : plus la livraison est rapide, plus le niveau du stock d'alerte peut être bas. Dans le cas de marchandises qui ne devraient à aucun moment être en rupture de stock, une réserve généreuse pour les imprévus est calculée en plus des quantités de consommation typiques jusqu'à la livraison : le stock de sécurité.
Stock de sécurité :
Le stock de sécurité ert à absorber autant que possible les incertitudes et les ruptures d'approvisionnement. Idéalement, les délais de livraison retardés, les écarts entre le stock comptabilisé et le stock de l'entrepôt et les prévisions de demande incorrectes peuvent être comblés par un stock de sécurité.
Variations :
Lorsque le stock d'alerte est atteint, il est possible d'une part de réagir en commandant une quantité définie (« politique de taille de lot du point de commande »). D'autre part, il peut être judicieux de réapprovisionner le stock à un niveau de stock cible défini après chaque sortie de marchandises (« politique de niveau de stock au point de commande »).
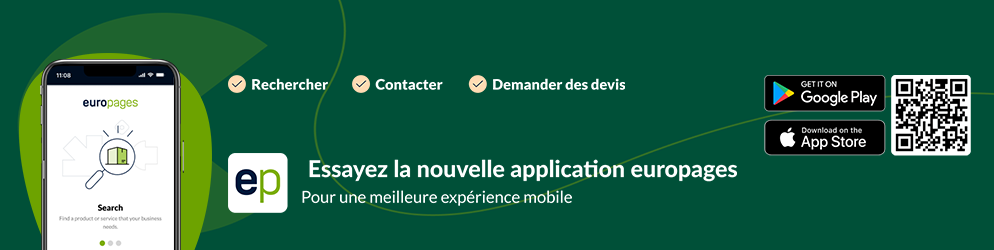
Calculer le point de commande - un exemple
Un constructeur automobile a besoin chaque jour de 1 000 volants pour la production de ses véhicules. Il ne les fabrique pas lui-même, mais il les reçoit d'un fournisseur selon ses spécifications. Le temps de transport des pièces est de quatre jours (délai de réapprovisionnement). Après la livraison, le client les soumet à un contrôle d'entrée des marchandises d'une journée. Il faut donc compter cinq jours au total pour que les volants arrivent du fournisseur à la production. Afin d'avoir un stock minimum sûr, le constructeur automobile calcule avec un tampon de trois jours.
Cela se traduit par un stock minimum de 3 000 volants (3 x 1 000 = 3 000).
Le point de commande (stock d'alerte) dans ce cas est de 8 000 volants. Il est composé d'une part du stock minimum de 3 000 pièces et d'autre part de la quantité de la consommation quotidienne (1 000 pièces) multipliée par le délai de réapprovisionnement de cinq jours.
3 000 (stock minimum) + 5 000 (1 000 quantité consommée quotidienne x 5 jours de délai de réapprovisionnement) = 8 000
Si le nombre de volants en production est inférieur à 8 000, le point de commande est atteint et du nouveau matériel doit être commandé.
La procédure du cycle de commande en détail
À bien des égards, la procédure du cycle de commande est similaire à la procédure de point de commande, mais il existe cependant des différences importantes.
Orientation vers les délais :
Contrairement à la procédure de point de commande, la procédure de cycle de commande n'est pas principalement axée sur la quantité, mais sur le délai. Cela signifie que de nouveaux produits sont commandés régulièrement à certains intervalles de temps.. Le moment de la commande concrète respective est donc indépendant du stock actuel.
Stock de sécurité :
Un stock de sécurité généreux est essentiel dans le cadre du processus de cycle de commande afin de pouvoir répondre aux augmentations inattendues de la demande.
Variations :
En principe, la méthode de cycle de commands offre deux possibilités pour la politique de commande. Les intervalles de commande et la quantité de commande sont déterminés. Cette variante est recommandée si l'expérience a montré que la consommation est principalement constante. C'est ce qu'on appelle la « procédure de taille de lot du cycle de commande ». Alors que la période de commande est fixe, la quantité commandée est ajustée individuellement. Cette méthode est particulièrement recommandée lorsqu'un fabricant livre plusieurs articles, afin de garantir la meilleure coordination possible. La méthode est connue sous le nom de « procédure au niveau de l'entrepôt du cycle de commande ».
Déterminer le cycle de commande – un exemple
Si le constructeur automobile supposé sous « Calculer le point de commande » (voir ci-dessus) travaillait selon le principe du cycle de commande, cela pourrait ressembler à ceci dans les mêmes conditions : pour sa production, il a besoin de 1 000 volants chaque jour. Afin de garantir la production, il commande automatiquement le premier de chaque mois une quantité correspondant au nombre de jours ouvrés dans un mois. Il s'agit d'un forfait de 20 000 pièces (cycle de commande).
Cependant, du fait que chaque semaine n'a pas cinq jours ouvrés et que d'autres variables peuvent survenir, il doit modifier la quantité commandée à certains intervalles, le cas échéant, afin de ne pas avoir trop ou trop peu de volants. Cela pourrait entraîner des coûts de rupture de stock. Afin de l'éviter, il est judicieux de vérifier régulièrement le niveau du stock. Cela permet de constater comment la consommation évolue et comment la quantité commandée doit être ajustée au moment de l'approvisionnement déterminé (à partir de la page 11).
Conclusion : les conditions individuelles de l'entreprise sont décisives
Les procédures de point de commande et de cycle de commande ont leurs avantages et leurs inconvénients spécifiques. Le système de commande utilisé dépend largement de la demande et des conditions d'achat des marchandises vendues. Il n'est pas toujours judicieux de se limiter à une seule des deux méthodes de commande. Dans la pratique, les deux procédures de commande sont souvent combinées.